
Capabilities
World class manufacturing, delivering quality parts at competitive price on time.
FDM
Fused Deposition Modeling is a widely used and effective 3D printing technology that is particularly well-suited for prototyping and the production of small parts.
It is relatively simple and inexpensive, and the materials used in FDM printing are widely available and relatively cheap. FDM is also capable of producing strong, durable parts with good mechanical properties.
Maximum build size: 1000 mm x 1000 mm x 1000 mm
Standard lead time: 4 business days
Dimensional accuracy: ± 0.0015 mm of Tolerance
10+ Material options available
20+ Colour options available

SLA
Stereolithography is a powerful and effective 3D printing technology that is particularly well-suited for producing high-resolution and intricate parts with smooth surface finishes. One of the main advantages of SLA 3D printing is its ability to produce parts with high accuracy and fine details.
Maximum build size: 1000 mm x 1000 mm x 1000 mm
Standard lead time: 4 business days
Dimensional accuracy: ± 0.0015 mm of Tolerance
10+ Material options available
20+ Colour options available

SLS
Selective laser sintering is a widely used and effective 3D printing technology that is particularly well-suited for producing functional parts and prototypes.
It is capable of producing strong, functional parts with good mechanical properties. The materials used in SLS printing are also widely available and relatively inexpensive. Additionally, SLS does not require support structures, as the excess powder around the object acts as a support.
Maximum build size: 400 mm x 400 mm x 450 mm
Standard lead time: 5 business days
Dimensional accuracy: ± 0.02 mm of Tolerance
Custom colour options available

DMLS
DMLS is capable of producing complex, highly detailed metal parts with good mechanical properties. The materials used in DMLS printing are also widely available and relatively inexpensive. Additionally, DMLS does not require support structures, as the excess powder around the object acts as a support.
Maximum build size: 400 mmx 400 mm x 400 mm
Standard lead time: 10 business days
Dimensional accuracy: ± 0.015 mm of Tolerance
Materials: Aluminium, SS 316, Titanium
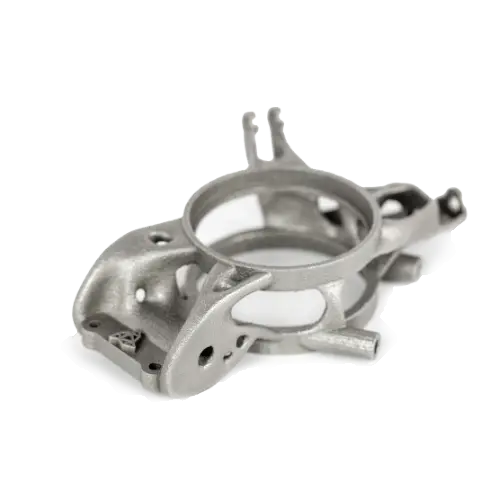
DLP
DLP is capable of producing highly detailed and accurate parts with smooth surface finishes. The resin used in DLP printing is also available in a wide range of colors, making it well-suited for producing finished, visually appealing parts.
Maximum build size: 277 mm x 156 mm x 400 mm
Standard lead time: 5 business days
Dimensional accuracy: ± 0.075mm of Tolerance
5+ colour options available
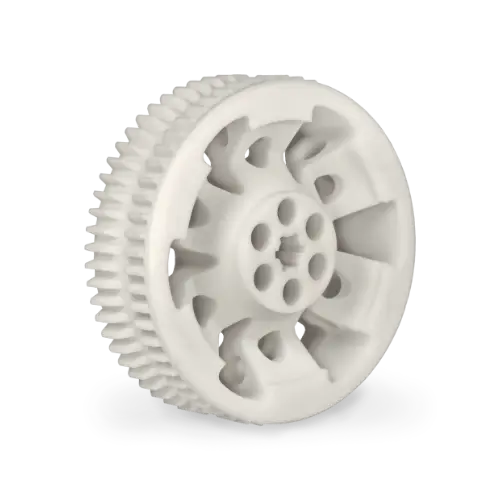
MJF
MJF delivers functional plastic parts with isotropic mechanical properties that can be used for detailed prototyping or end-use low-volume production.
Maximum build size: 380 mm x 284 mm x 380 mm
Standard lead time: 5+ business days
Dimensional accuracy: ± 0.01 mm of Tolerance
Custom colour options available

3D Printing
Milling
CNC mills are ideal for geometric designs and needs for quick production. From prototyping to mass production, you can create very accurate, high-quality products. Our CNC capabilities include mills with 3 axis, 3+2 axis, and full 5-axis milling centers.
Maximum Machine size
-
Working Area: 800 cm x 500 cm x 500 cm
-
Table Size: 2400 cm x 810 cm
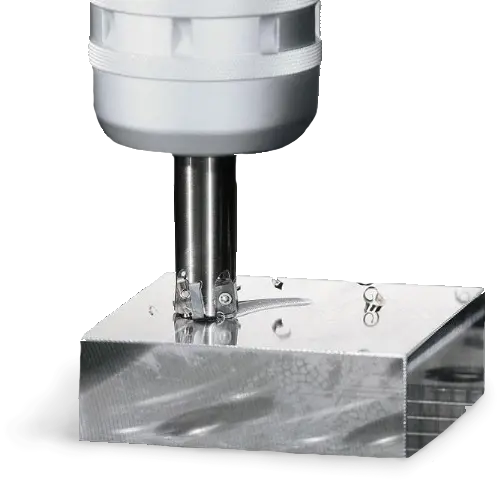
Turning
CNC turning is a process in which an automated lathe shapes a rotating workpiece. Precise, repeatable, and scalable.
CNC turning is ideal for creating parts with simple geometries and rounded or cylindrical shapes, as part of high-volume production runs.
Surface treatment: Heat treatment and Shot blasting.
Finishing Available: Powder coating, Anodizing, Sand Blasting, Bead Blasting, Teflon Coating, PVD Coating
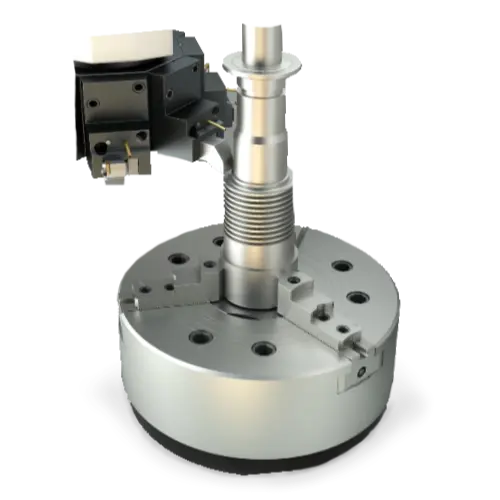
EDM
EDM is a specialized type of CNC machining. Electricity is pulsed in a controlled manner to precisely erode even the hardest metals. When working with hardened tool steels, this is critical. When done properly, the surface finish is mirror-smooth and doesn't require additional polishing.
Maximum Machine Dimension
-
Working Area: 2800 mm x 1300 mm
-
Table Size: 1650 cm x 800 cm x 800 cm
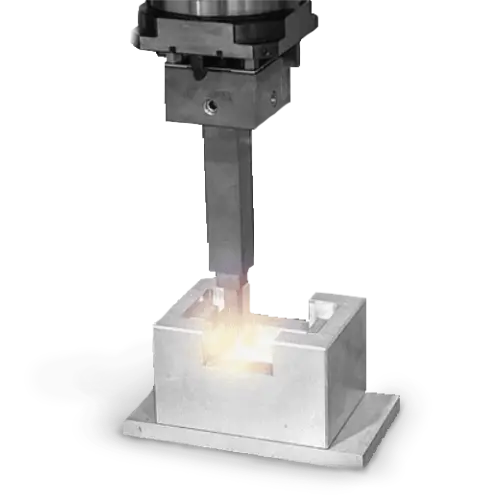
CNC Machining
Cutting
-
Laser Cutting: Laser cutting is a machining method that uses an intensely focused, coherent beam of light called a laser to cut through the material.
-
Waterjet Cutting: It is a manufacturing process that uses a water jet with high pressure coming from a small nozzle to cut through the material.
Maximum Working Range
4000mm X 1530mm X 765mm
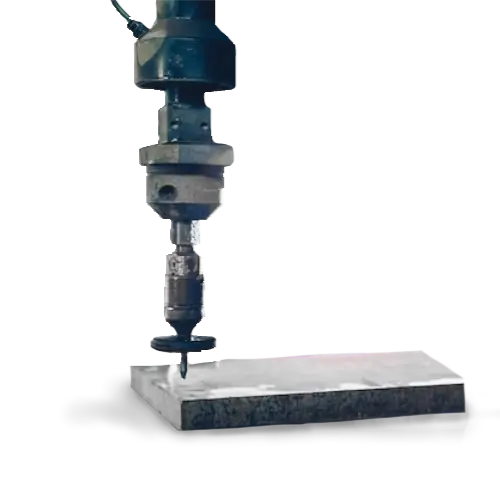
Sheet Metal Bending
Sheet metal bending is an operation that involves using forces to change the shape of a sheet. This is done to achieve the desired form or shape needed for a manufacturing process.
Maximum Press Capacity: 1600 kN
Maximum Table Length: 3100 mm
Maximum Sheet Thickness: 8 mm

Sheet Metal Punching
Sheet metal punching is a cutting process in which material is removed from a piece of sheet metal by applying a great enough shearing force.
Material: Aluminum, Copper, Titanium, Stainless Steel, Brass
Maximum Sheet Thickness: 6 mm
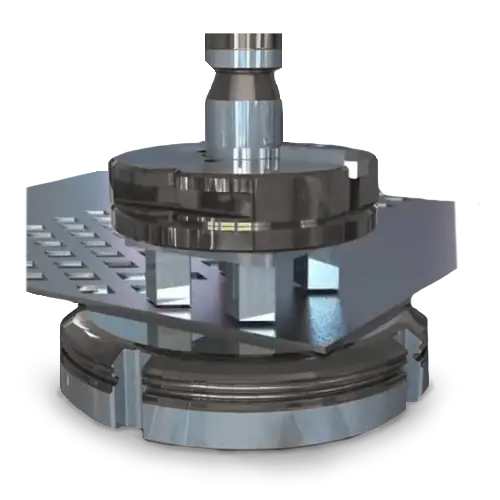
Assembly
The assembly of a sheet metal component is a process of combining various parts that make up the component and making each part correctly positioned, then fixed and connected so as to form a process that meets the requirements of the drawing.
-
Riveting: A rivet is a type of permanent mechanical fastener
-
Welding: It is a fabrication process that involves joining two metal sheets by forms of heat, pressure
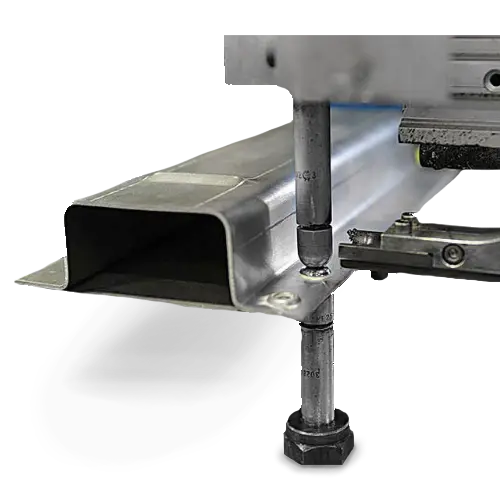
Sheet Metal Fabrication
Rapid Production
The process is extremely fast compared to other methods, and the high production output rates make it even more efficient and cost effective
Complex Part Designing
Manufacture extremely complex parts with its ability to make components in numerous quantities.
Choice of Material
According to the application, Injection molding can be performed with a wide range of materials.
Process Benefits
Rubber Moulding
Rubber Molding is a process of injecting raw rubber material into a metal mold cavity.
-
Over molding: Over molding is a multi-step injection molding process where two or more components are molded over top of one another.
-
Materials: Rubber, SAN (AS), Silicone, Thermoplastic elastomer (TPE), TPU.

Plastic Injection Moulding
Plastic injection molding is a process in which thermoplastic polymers are injected into a mold cavity to produce the final product.
-
Extrusion Molding: During the process, the material is melted and pushed through an extrusion molding machine, forming a long, tube-like shape or rod.
-
Insert Molding: Insert molding is a process which uses a preformed part that is loaded into a mold where it is then over molded with thermoplastic resin to create the final product.
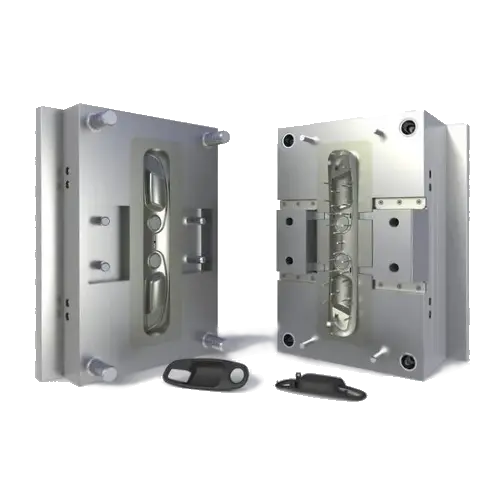
Injection Moulding
Process Benefits
Design Flexibility
Get design options that are not otherwise possible. RIM can accommodate small to very big parts, impart structural stability, strict tolerances, and a wider range of wall thicknesses within the same item. Also encapsulating other components.
Cost Efficiency
Aluminium moulds typically cost 70% less than steel moulds. Also, they last longer, since they are used at lower pressures and temperatures. They may never need to be replaced and can be modified at a lower cost.
Low Cure Time
The liquid polymers require less pressure (~100 psi) and lower temperatures (~90°). The exothermic reaction cures the part inside the mold. Cure times vary from less than a minute to several minutes.
Capabilities
-
Cavity Pressure: 15 psi - 30 psi
-
Tooling Options
-
Prototyping (Composite Moulds)
-
Ribs/Bosses can be molded in for stiffness
-
Inserts can be molded in for attachments

Reaction Injection Moulding
Reaction Injection Moulding (RIM) is a technique used to create intricate, very durable plastic parts with a smooth surface finish.
RIM's capacity to create huge, complicated pieces with a high level of dimensional precision and a flawless surface finish is one of its key benefits.
Types of Reaction Injection Molding
1. Structural Reaction Injection Molding (SRIM)
2. Reinforced Reaction Injection Molding (RRIM)
Process Benefits
Smooth Finish
Investment casting uses a ceramic mold that produces very smooth finishes, typically averaging 125RA surface finish as a cast.
Wide size range
Investment casting allows for both large and small casts. From miniature parts that are 1/10 of an ounce, to large parts that are 50 pounds can be produced.
Affordable tooling
Investment casting requires less expensive equipment and is inherently less dangerous, which allows for costs to remain low
Materials
-
Carbon Steels.
-
Low Alloy.
-
Alloy Steel.
-
Austenitic Stainless Steel.
-
Ferritic Stainless Steel.
Investment casting is a manufacturing process in which a wax pattern is used to shape a disposable ceramic mold. A wax pattern is made in the exact shape of the item to be cast. This pattern is coated with a refractory ceramic material. Once the ceramic material is hardened, it is turned upside-down and heated until the wax melts and drains out. The hardened ceramic shell becomes an expendable investment mold. Molten metal is poured into the mold and is left to cool. The metal casting is then broken from of the spent mold.

Investment Casting
Fast Time to Market
Quick production of both prototypes and products. This speed reduces the time spent in the prototyping stage of production, hastening the time to market.
Increased ROI
Recoup your investments in a short time. Lower production and prototyping costs reduce the time spent getting your ROI because you incur fewer expenses.
Reduce Processes
Complex assembly processes can be consolidated into one process.
Process Benefits
Soft Tool
Soft tooling is a cost-effective method of tooling, popular for use with cast urethane molding, that allows manufacturers to produce medium to low volumes of parts at speed. Silicone is the most common soft tool material for cast urethane and is an ideal manufacturing process for prototyping and low-volume production runs. One of the advantages of soft tooling is that its material requirements are flexible, meaning manufacturers can use materials without worrying too much about compatibility.
Materials: Soft Steel, Nickel Alloys
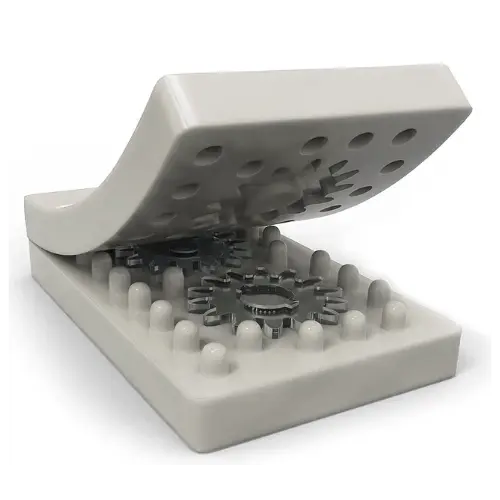
Hard Tool
Hard tooling is a method of tooling often used for injection molding. Hard tools are made of durable metals — such as steel or nickel alloys — that can withstand multiple production cycles, allowing manufacturers to quickly produce high volumes of parts. When manufacturers have strict tolerances, testing requirements, and function standards they must adhere to, it makes more sense to use hard tooling over soft tooling. This tooling type is ideal for producing durable high-precision parts.
Materials: Soft Steel, Aluminium

Rapid Tooling
Low Volume Manufacturing
When volumes do not justify investment in injection molding and short-run production parts, it can complete weeks before production tooling is ready.
Functional Testing
It can be used to do function testing before testing the mass production products and issue reports or even get any certification approval.
Color & Texture Studies
If you are unable to decide a color for the part, you can produce 10-15 models and get them colored with the ones of choice and select the aesthetic.
Capabilities
Materials
-
ABS: Acrylonitrile butadiene styrene is popular due to its low production cost.
-
PP: Polypropylene is one of the most widely used plastics and is very easy to mold.
-
PC: Polycarbonate offers high impact resistance and is available in transparent variations.
-
Glass filled material: Glass filled polymers increase structural strength, impact strength, and rigidity.
-
Wax: Wax can be formed into nearly any form imaginable and offers the ability to create surface textures.
-
Rubber: Rubber-like materials are tough and have good tear strength. They’re ideal for gaskets and seals.
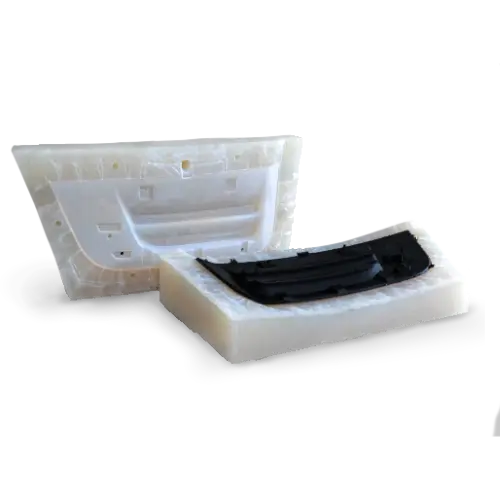
Maximum Housing Dimension: 1930 mm x 1510 mm x 900 mm
Maximum Mold Size: 750 mm x 900 mm x 750 mm
Vacuum Casting
3D Printing
3D printing is an additive manufacturing process where materials are joined together to make objects from 3D model data (CAD).

CNC Machining
Computer Numerical Control machining, is a widely used manufacturing process that uses automated, high-speed cutting tools to form designs from metal or plastic stock
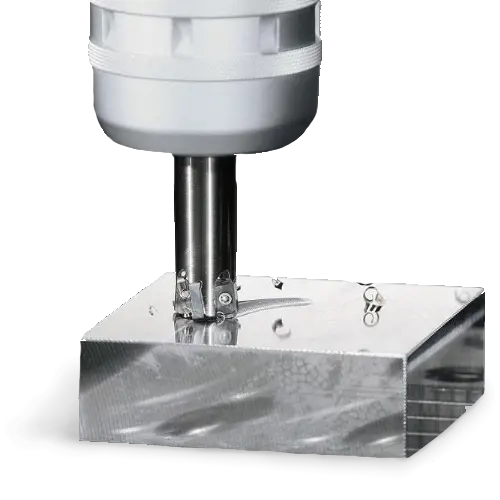
Sheet Metal Fabrication
Sheet metal fabrication is a subtractive manufacturing process that forms parts from thin metal sheets.

Vacuum Casting
Vacuum casting is a manufacturing that involves creating a mold of the desired part and then injecting liquid plastic or metal into the mold under a vacuum.
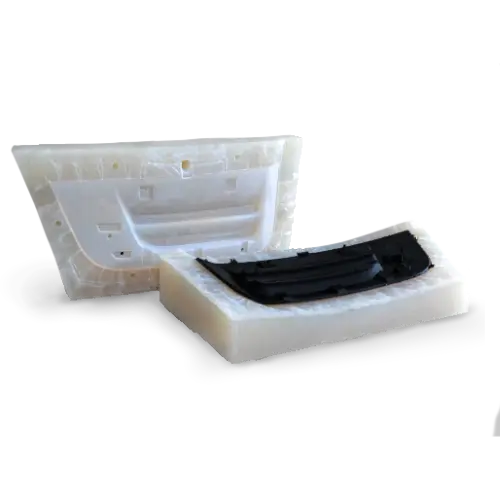
Injection Moulding
Injection molding process involves injecting molten plastic into a mold tool, then ejecting the solidified part.
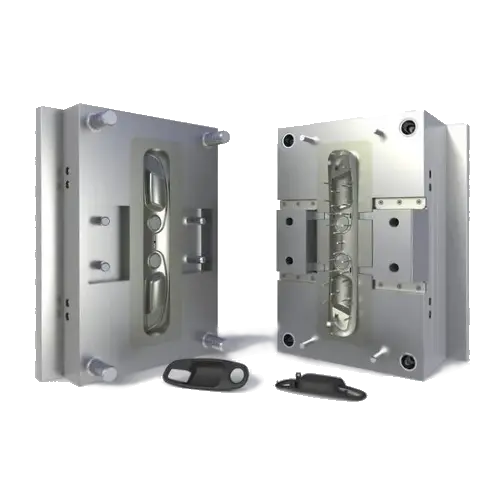
Reaction Injection Moulding
RIM is a technique used to create intricate, very durable plastic parts with a smooth surface finish

Investment Casting
Investment casting is a manufacturing process in which a liquid material is poured into a ceramic mold, which contains a hollow cavity of the desired shape, and then allowed to solidify.
